Center for Technology Transfers in Ceramics
Ceramic Innovation for Industry
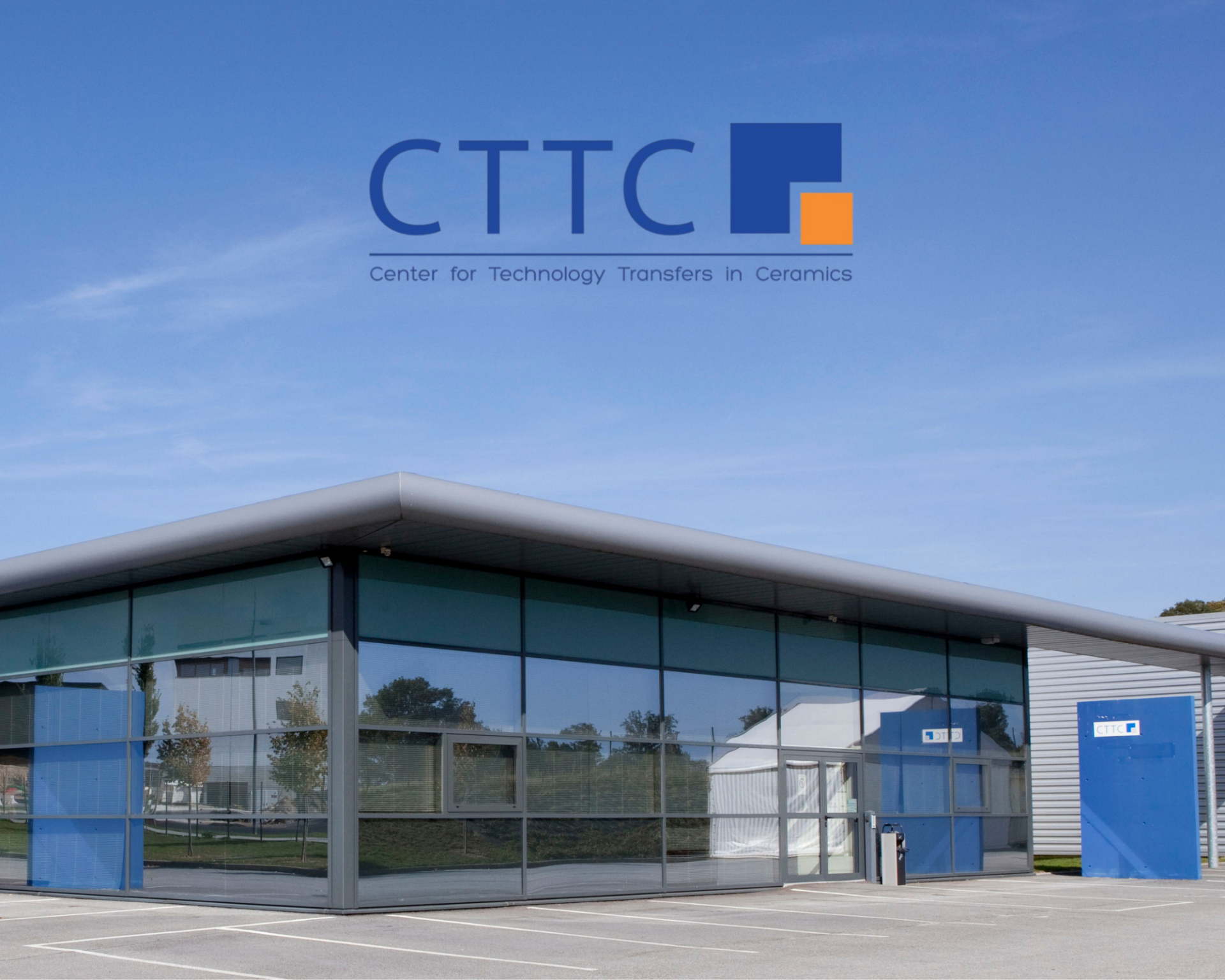
+
1000
projects
+400
customers
+
90
equipment
92
%
level of satisfaction
Since 1984
Our missions
As an association, the CTTC carries out missions of general interest to companies. It applies/develops, alone or in collaboration, ceramic shaping technologies that can be transferred industrially.
On the one hand, its strong links with academic research enable it to keep in touch with the state of the art in science and to position itself in the maturation of high-potential technologies, and on the other hand to offer industry its resources, expertise and the skills of its team.
Services
Our services
From materials characterisation to process industrialisation, including prototyping and training, the CTTC offers a wide range of services.
Our values
Whether it's our private activities (serving our customers), our collaborative activities (responding to a common need), or our internal developments (in the public interest), we are driven by the same values of responsiveness, flexibility, integrity and professionalism.
Our multi-skilled team is made up of men and women who are experts in their fields, combining their skills to meet both the demands expressed by our customers and the economic, social and environmental challenges we now face.
Thanks to our know-how, our experience feedback and the range of technologies at our disposal, we can turn ideas into reality while covering a wide range of needs, within deadlines adapted to our customers' and partners' deadlines and in strict compliance with confidentiality rules.
Reactivity
Flexibility
Professionnalism
Integrity
Blog
Our news
OUR AGENDA
They share their experiences
We've only worked with the CTTC once, in order to solve a technical problem involving the durability of ceramic parts. The CTTC quickly assessed our parts and gave us the right solutions to eradicate our breakage problem [...] which had a very positive impact on our customers.
The people I dealt with at the CTTC demonstrated great expertise, excellent responsiveness and a very good sense of customer relations.
The results of CTTC's action, 6 months later, are clearly positive. We have identified new ways of developing our products and strengthened the quality of our customer/supplier relationships.