Our technological resources
Our technological resources include 1,500 m² of technological facilities at the ESTER technology park in Limoges. This infrastructure includes an advanced manufacturing platform, an additive manufacturing platform, a materials characterization laboratory and a FabLab.
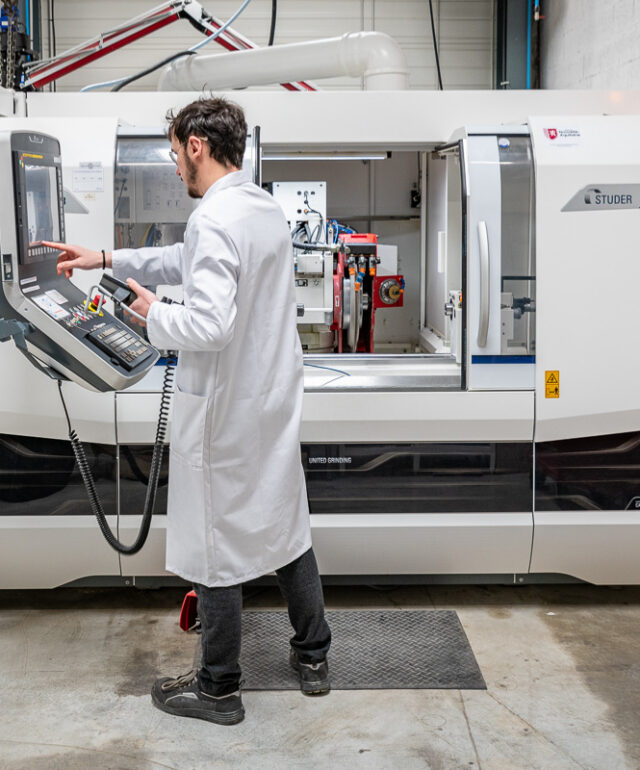
Advanced manufacturing
Our CERATECH by CTTC platform gathers a range of resources for the manufacturing of technical ceramics or multi-material.
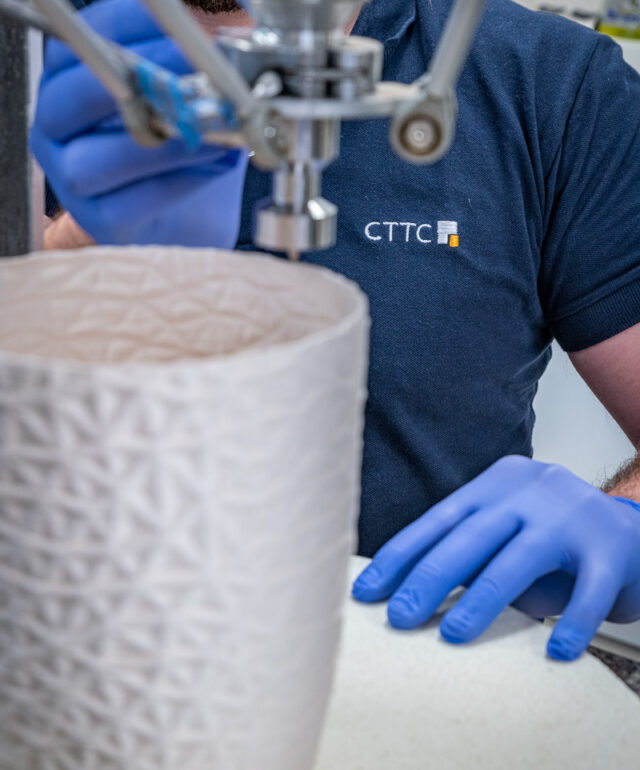
Additive manufacturing
Our ALTERINOV by CTTC platform comprises a dozen printers, applying single or hybrid process for 3D printing or direct ink writing.